I'm not sure if bendorsey's Rotary Coal Transfer has been used in any routes available from the Download Station. If not it's a pity because it is a great piece of kit.
I'm working on the next iteration of "Urban IndustRail". It includes a loop to the north that incorporates Alexander grain terminal:
And a small mineral working:
The route then heads south into a grimy dirty industrial precinct once more, and it is here that I have used bendorsey's the rotary coal transfer:
Now, that's certainly not the way it is intended to be used. As set up by bendorsey, loaded narrow gauge coal cars use the upper level. A coal car is positioned between those two big cog wheels, secured to the tack, and a cable actuating mechanism pulls the cog wheels so that they move up the rack strips. In the process the track on which the freight car is resting rotates, inverting the freight car over a hopper so that the coal is transfered into standard gauge cars underneath.
While the device is not animated, all the intricate workings are shown in amazing details.
I've actually used the device to dump ore from the Alexander mine into the hopper that feeds a calcification and cementation plant (sounds good, but don't ask me to explain what it does!).
Now if anything is worth using, it's probably worth using twice.
Here specially selected logs are unloaded onto a conveyor at XL-Ent Furniture:
In both locations a ProtoLARS section of track is used on the transfer table. This is an ideal application for ProtoLARS:
1. ProtoLARS is height adjustable (most other industry tracks are not).
2. It can be configured so that unloading takes place after a pre-set time.
3. The locomotive can be uncoupled and moved away before unloading occurs.
Test and packaging of the extension to IndustRail is under way. On the Download Station next week, possibly.
Phil
I'm working on the next iteration of "Urban IndustRail". It includes a loop to the north that incorporates Alexander grain terminal:
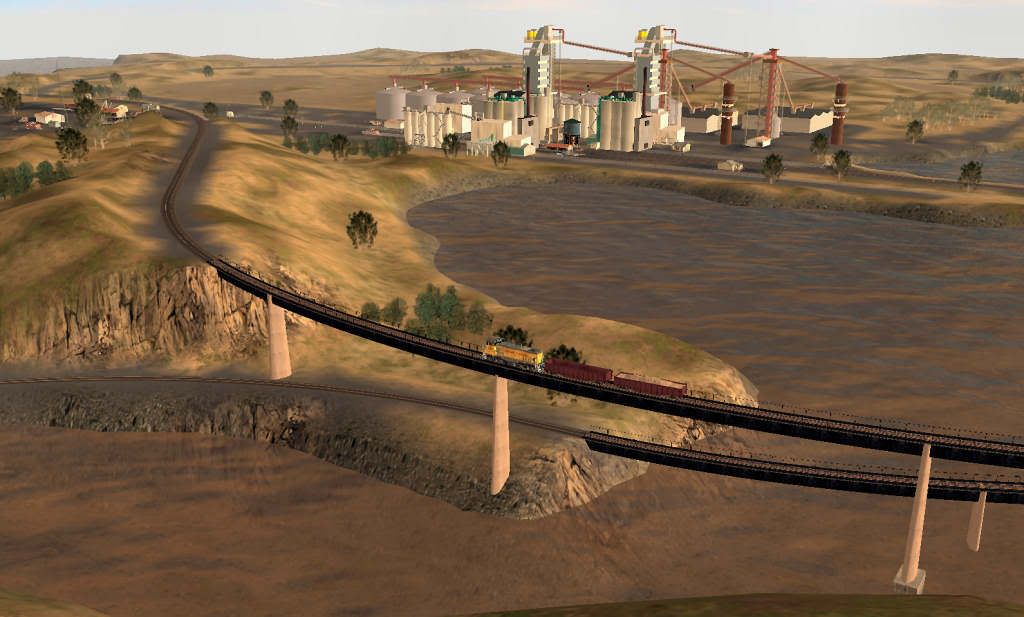
And a small mineral working:
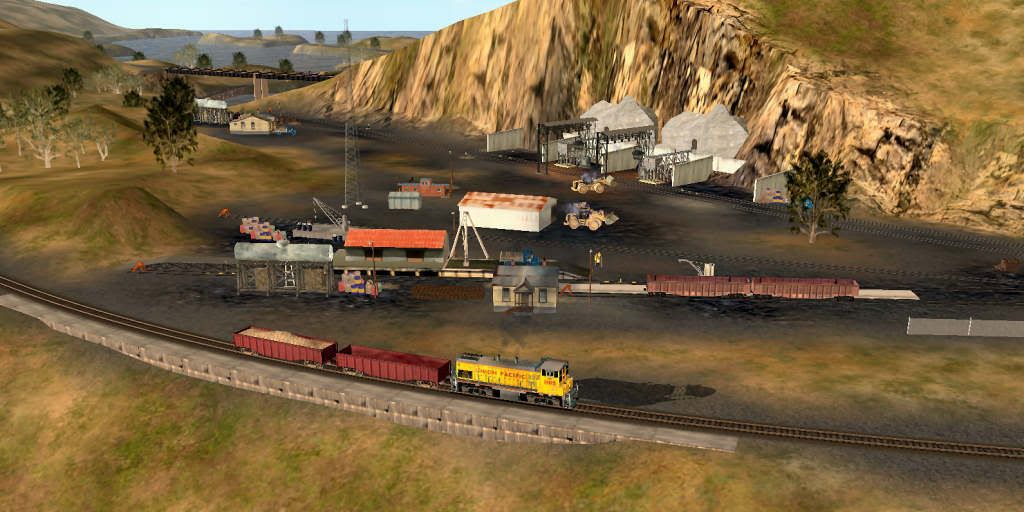
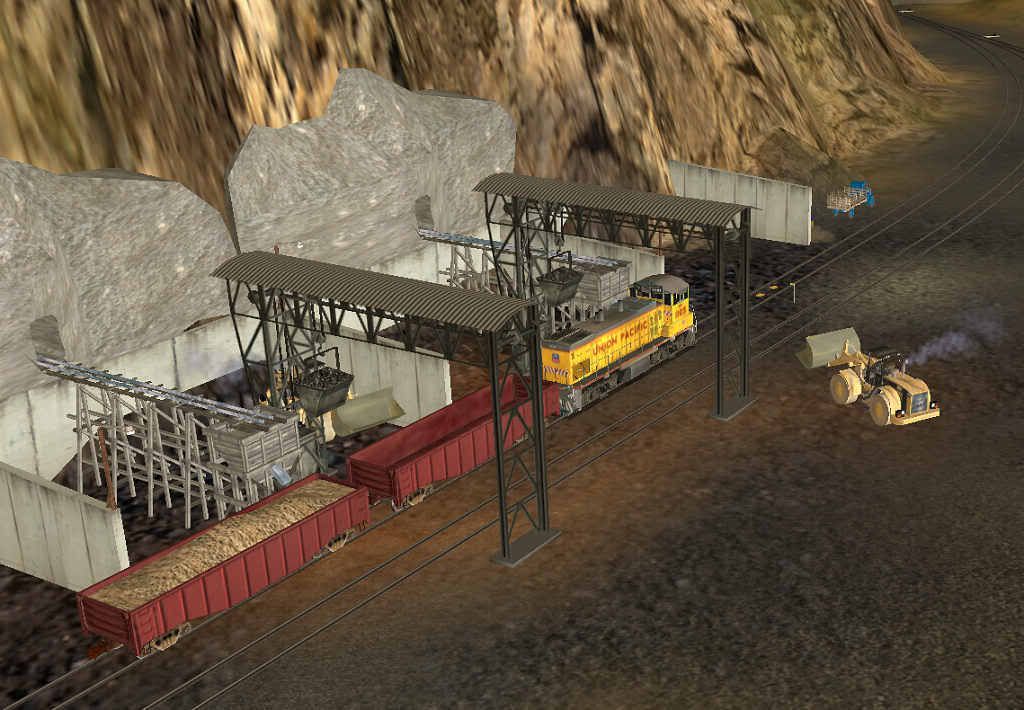
The route then heads south into a grimy dirty industrial precinct once more, and it is here that I have used bendorsey's the rotary coal transfer:
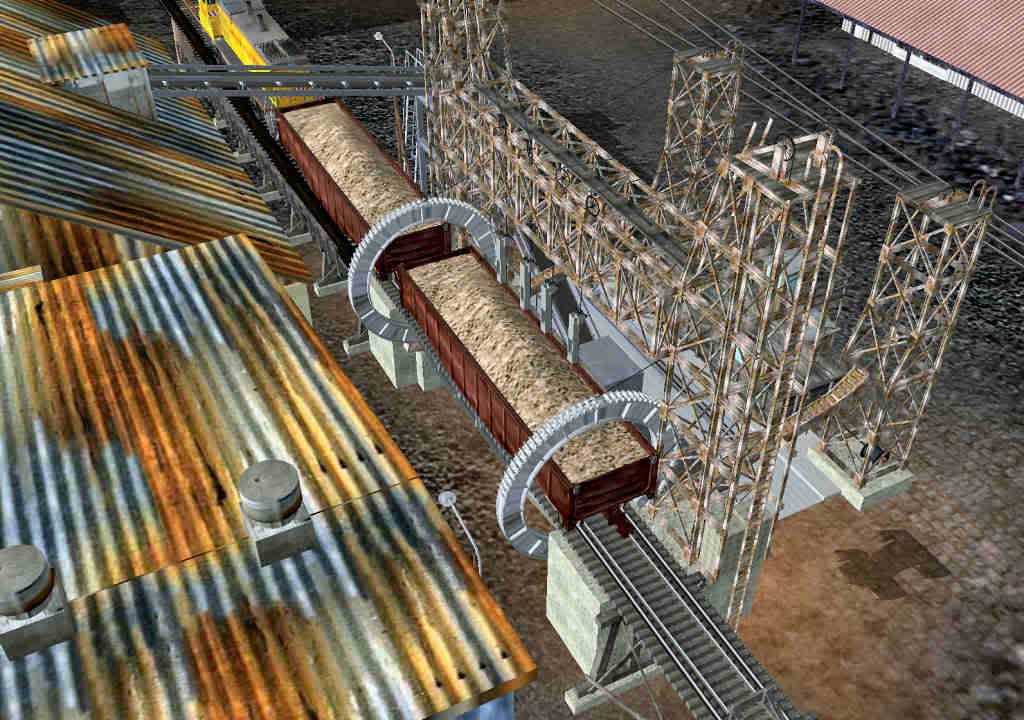
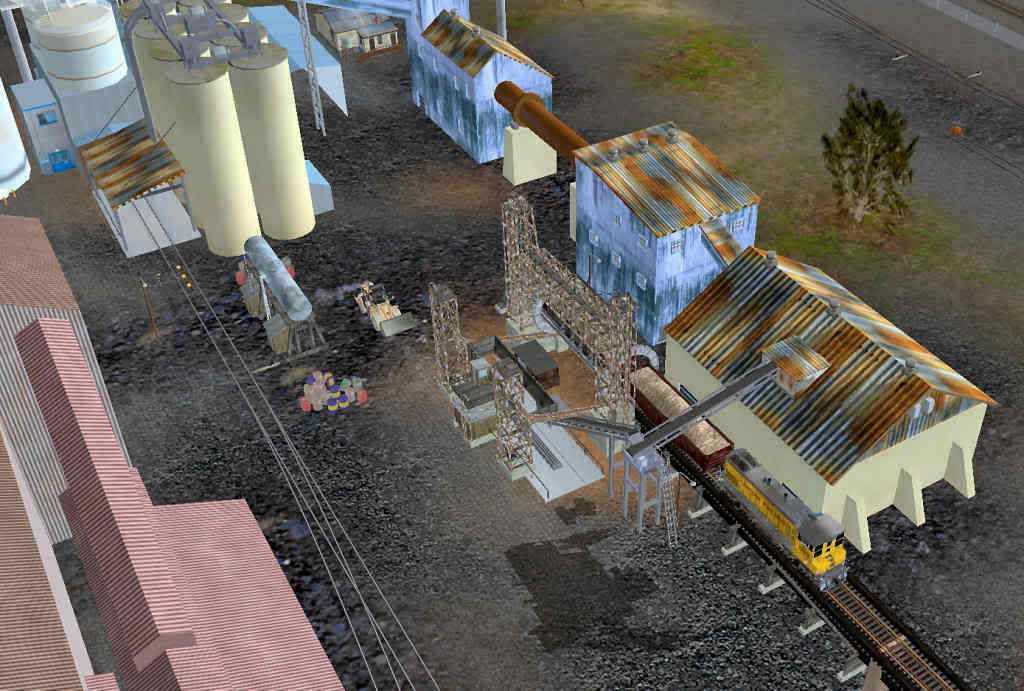
Now, that's certainly not the way it is intended to be used. As set up by bendorsey, loaded narrow gauge coal cars use the upper level. A coal car is positioned between those two big cog wheels, secured to the tack, and a cable actuating mechanism pulls the cog wheels so that they move up the rack strips. In the process the track on which the freight car is resting rotates, inverting the freight car over a hopper so that the coal is transfered into standard gauge cars underneath.
While the device is not animated, all the intricate workings are shown in amazing details.
I've actually used the device to dump ore from the Alexander mine into the hopper that feeds a calcification and cementation plant (sounds good, but don't ask me to explain what it does!).
Now if anything is worth using, it's probably worth using twice.
Here specially selected logs are unloaded onto a conveyor at XL-Ent Furniture:
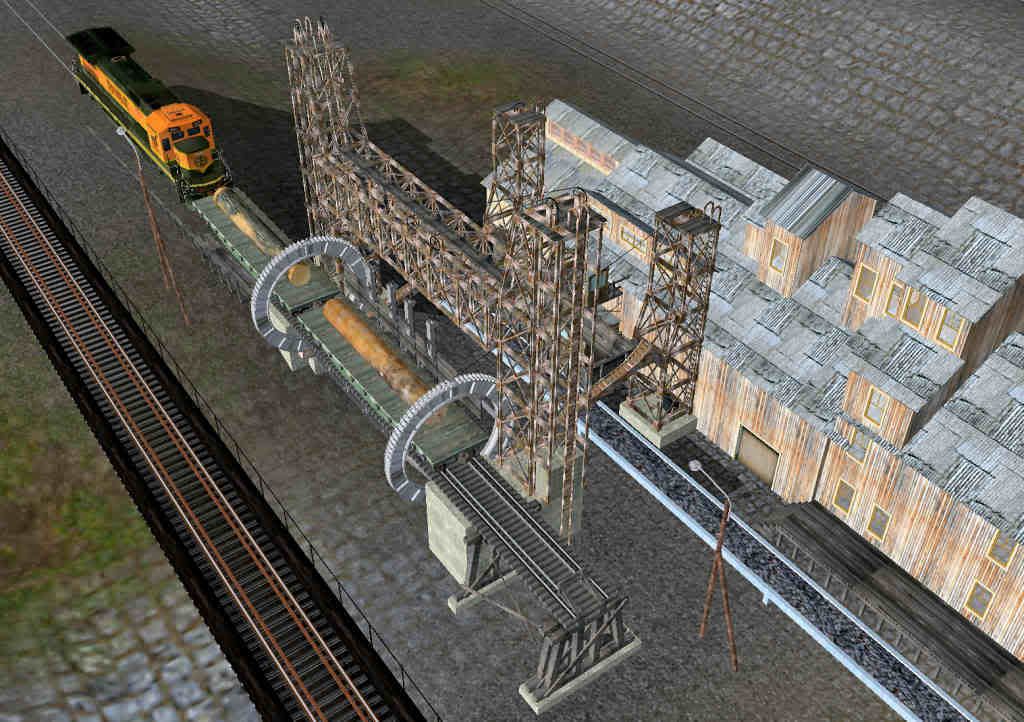
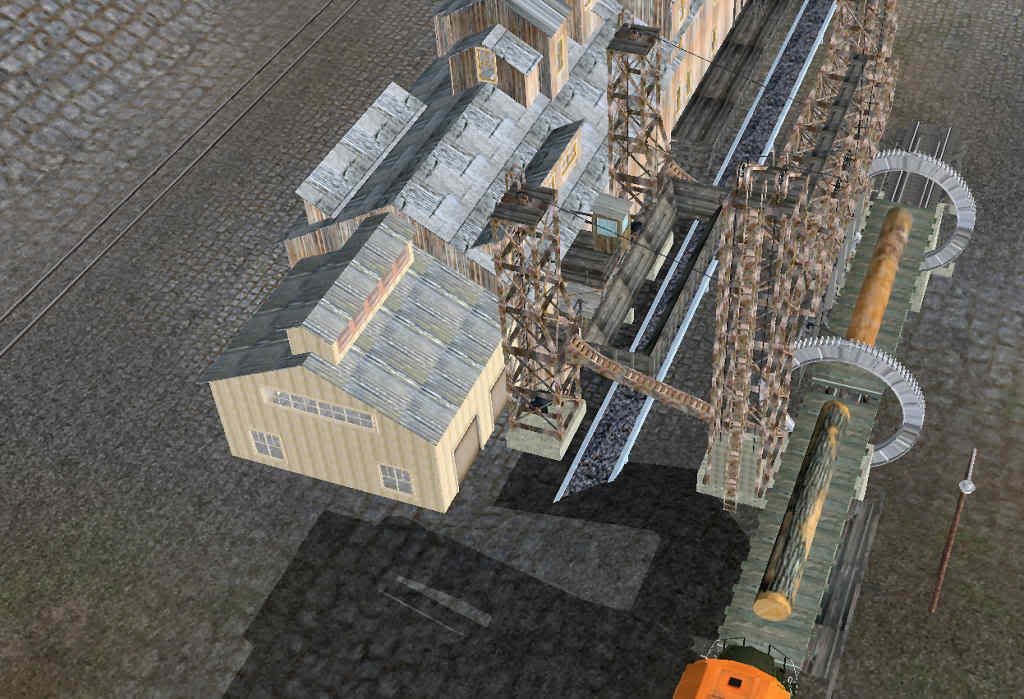
In both locations a ProtoLARS section of track is used on the transfer table. This is an ideal application for ProtoLARS:
1. ProtoLARS is height adjustable (most other industry tracks are not).
2. It can be configured so that unloading takes place after a pre-set time.
3. The locomotive can be uncoupled and moved away before unloading occurs.
Test and packaging of the extension to IndustRail is under way. On the Download Station next week, possibly.
Phil